As you will be well aware, prolonged periods of cold weather (especially sub-zero temperatures) will adversely impact the smooth running of your compressed air systems, but you may not know what steps to take to help! Fear not, as our expert team at Rotonair has compiled this guide to ensure operations are protected this winter, and your air supply remains optimised no matter what the great British weather throws at us!
The best place to start is with maintenance. As a business owner or facility manager, it is essential to ensure your compressor installation is regularly well-maintained.
Doing so will prepare your equipment for freezing winter temperatures, reduce the risk of decreased efficiency, costly downtime, and interruptions to productivity, and even extend the lifespan of your compressed air equipment.
It makes financial and business sense to schedule regular maintenance to prevent issues like expensive air leaks. Please don’t hesitate to contact us for advice on our cost-effective support services and packages.
In this blog, we’ve collated practical maintenance tips, cold-weather checks, preventative measures, and recommendations to help protect your air compressor installation in these colder spells and over festive shutdown periods.
By following these tips, you can help safeguard your air compressor from damage, minimise unnecessary downtime, reduce repair costs, and ensure your compressor operates at peak performance year-round, especially during colder months.
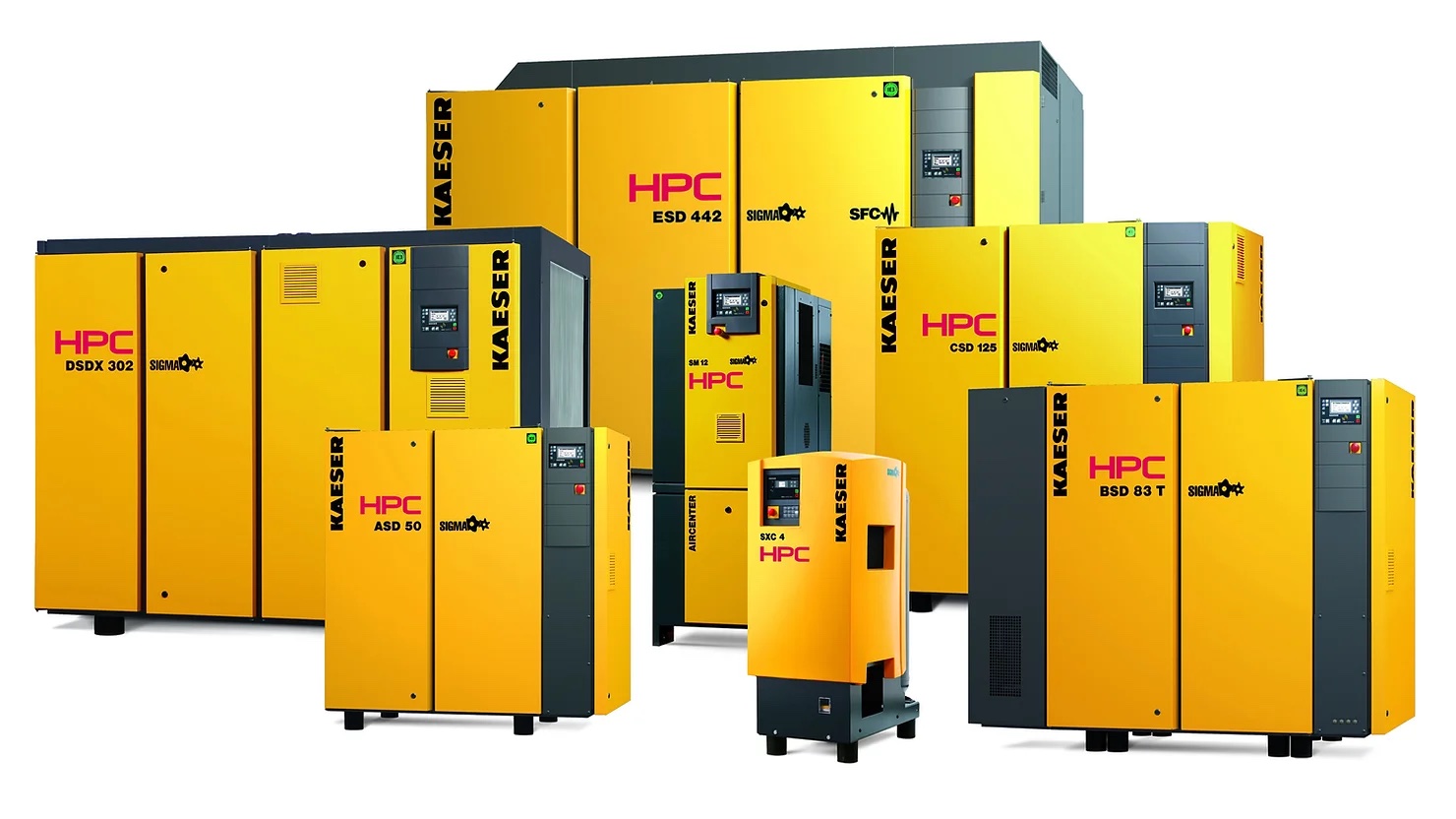
Safety Measures
The ideal ambient temperature for an air compressor is 5°C to 40°C. Running it in colder temperatures may lead to unexpected and costly breakdowns.
A rotary screw compressor may have an alarm that prevents it from starting up if the ambient temperature is too cold.
Consider cost-effective and safe measures to ensure your air compressors are well-heated and insulated throughout the year.
Drain Moisture
In cold temperatures, condensation can accumulate in air compressor systems, leading to moisture build-up.
Regularly draining moisture from your compressor’s air tanks is crucial to prevent it from freezing and accumulating in condensate lines.
Turn Up The Heat
Trace heating provides controlled heat to pipelines and vessels, particularly important when an air compressor is connected to a refrigerated air dryer.
In such applications, the dryer’s temperature could drop below the dew point, forming condensate.
As mentioned above, it is essential to ensure that compressor rooms and outlets are well-sealed and well-heated. Consider additional heating during freezing weather.
Exterior pipework can freeze in freezing weather; this can be avoided by lagging your pipework.
If a room is too cold for refrigerated air dryers, the moisture extracted can freeze inside the machine, potentially causing a blockage and internal damage. Again, extra heating is needed when the temperature is low.
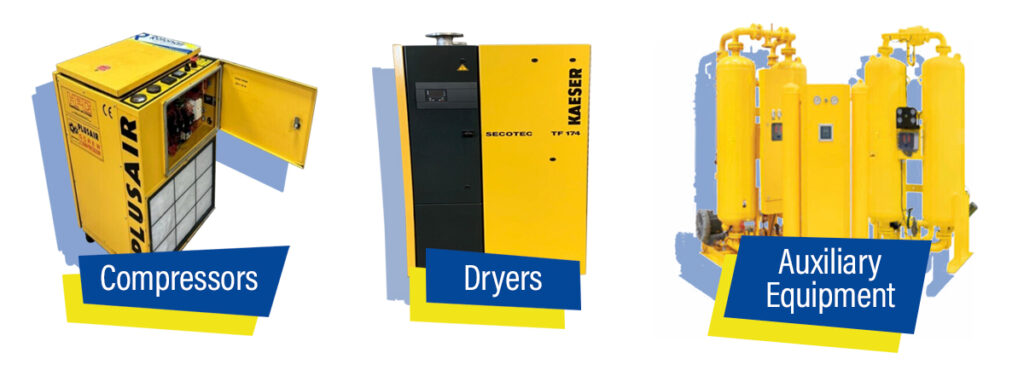
Synthetic Lube
During cold weather, the air compressor oil may thicken and become less effective as a lubricant. This can increase the pump’s power requirements, deplete the supply, and affect the motor’s lifespan.
Depending on the application, a synthetic lubricant may be a better choice during colder weather, as it is less likely to thicken in freezing conditions.
Check Openings
During wet or windy weather, ensure the compressor’s air intake openings are protected from excessive rain or snow blowing in from the outside.
If the air compressor’s openings are left vulnerable to the elements, they could lead to issues such as saturating the air filter or forming ice on the air intake.
Insulate Air Lines
Proper airline insulation is essential to prevent any disruption to compressed air flow and potential damage to the compressor system.
Choose an appropriate insulation material for the temperature range and environmental conditions. Please don’t hesitate to contact us if you need support with this.
Protecting your air compressor from damage during the colder months of the year will result in a reduction in repair expenses, plus dependable performance from your compressor in the long run.
Feeling Drained
Ensure that compressed air receivers (pressure vessels) are regularly or continually drained to avoid the risk of moisture or any build-up of compressor condensate freezing in winter. Freezing condensate can cause filter blockages. Also, drain traps should not be left open, as doing so can introduce cold air and impurities into the system.
If you have an automatic draining system, check that it’s working before winter sets in.
Electronic zero-loss condensate drains automatically discharge any moisture from receivers, compressed air dryers and system components to help ensure condensate does not enter pipework distribution systems. Most electronic models feature a test button that should be used periodically throughout the year and more regularly in winter to check that the drain is functioning correctly.
Condensate management products should always be included in preventative maintenance agreements.
If your system has manual condensate drains, they should be checked weekly and operated when necessary.
Remember that very cold or sub-zero temperatures can result in less effective moisture control measures, which could lead to moisture carry-over and corrosion.
Be aware that a noticeable increase in the condensate can indicate a more severe system issue.
Be Prepared
A backup air compressor and generator can be lifesavers in bad weather, allowing you to continue production, come what may.
Another good investment is a heat recovery system, which can capture warm air produced by the air compressor and used to heat the factory or the compressor room.
Regular Check-Ups
It is essential to have your compressor installation or compressed air system serviced by qualified engineers who use genuine spare parts (recommended by the manufacturer). This ensures long-term efficiency and reliability throughout the seasons, giving you the security of a well-maintained system.
Don’t underestimate the power of professional preventative maintenance. It’s the key to ensuring your system is expertly serviced and remains in optimal condition, especially when facing the challenges of the cold winter months.
While you can always take advantage of our 24/7 emergency call-out service, preparing your system in advance is more cost-effective and less stressful. Time spent checking and protecting your system from potential issues could save you trouble later.
When you need expert advice, the friendly team at Roton Compressed Air is always here to support you. Whether it’s scheduling a winter service and check-up for all your compressed air and associated equipment or a series of maintenance throughout the year, we’re here to help, making your maintenance needs more convenient and manageable.
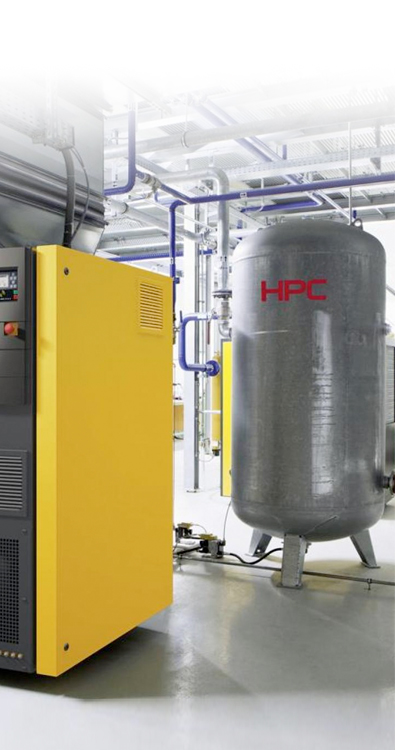
Winterise External Condensate Drain Lines & Bowls
Unprotected external condensate drain lines can lead to frozen pipes, which may result in your compressor operating slower or not working at all. If your system has condensate drain lines or bowls that may be exposed to sub-zero temperatures, use heat trace tape and insulation to protect them from freezing.
Any external pipework should always be fully insulated and protected from temperature extremes. Remember, heat trace tape requires power to protect from freezing. Keep this in mind if you are shutting down your system over the festive period or if any of your equipment is likely to be turned off due to reduced seasonal production demand. In this instance, drain any moisture from the lines in advance to help avoid freezing.
Temperature, Ventilation & Louvres
It is essential to minimise the amount of cold air around the compressor inlet to ensure your compressor can achieve its proper operating temperature as quickly as possible. This helps ensure proper lubrication, minimises moisture formation inside the compressor oil circuit for the compressor outlet and increases service life.
Thermostatically controlled louvres are highly recommended to maintain and optimise ventilation automatically throughout the year. Alternatively, you will need to manually adjust the inlet louvres to your compressor to reduce exposure to volumes of cold air.
Heat recovery applications provide an opportunity to reduce costs and recover up to 76% of the energy used to generate compressed air. While heat recovery systems vary, the simplest and most effective winter application involves ducting the hot air from the compressor outlet and recirculating it back into the compressor room to keep the system from running too cool.
Alternatively, the warm air can be ducted to an adjacent room to help reduce energy/heating costs.
Ambient & Compressor Cabinet Heaters
The ambient temperature of your compressed air system’s compressor house or installation should always be above freezing to ensure its performance, efficiency, and reliability.
Some products and equipment may be prohibited if the ambient temperature drops below the manufacturer’s minimum recommended operating parameters.
Most modern compressors can be equipped or retrofitted with optional cabinet heaters to pre-heat and help maintain the lubricant’s temperature. Ambient heaters can also be utilised in the compressor house. These heaters help ensure the lubricant remains above its minimum allowable temperature to help prevent cold starts that can cause premature wear, impacting the efficiency and service life of the motor.
If your compressor installation features cabinet or ambient heaters, adjust them for the lowest operating temperature recommended by your compressor manufacturer and regularly check to ensure they are operating and functioning correctly.
Maintaining System Components
Some plants reduce production over the winter months, while others may shut down over the festive period for preventative and planned maintenance. This break provides an ideal opportunity to inspect separators, valves, and condensate drains within a system susceptible to moisture.
Proper maintenance, cleaning, and repair during a winter shutdown will keep valves from sticking and condensate from freezing. Filters should be replaced as part of routine maintenance, which is particularly important in winter. In cold weather and periods of low temperatures, compressor lubricant can thicken and circulate slowly, requiring your compressed air system to work harder to continue to produce high-quality compressed air. Maintaining and replacing filters can help to combat the effects of thicker oil.
Expert Support, Specialist Advice & Professional Assistance
Roton Compressed Air offers expert support and advice for all air compressors and compressed air equipment brands. Our specialised compressed air engineers are multi-skilled, factory-trained professionals with extensive experience installing, servicing, and maintaining compressed air systems year-round in any location or environment.
With winter approaching and temperatures dropping, now is the perfect time to thoroughly inspect your compressed air system. Consider scheduling a general service to ensure your system is in peak condition and ready to handle the challenges of the harsh British winter!
Our cold weather check-list:
- Ensure the air receiver is empty of moisture daily.
- Keep up with maintenance. Check the compressor and components daily for moisture and ice build-up. This should include pipework, filters, dryers, drains, oil water separators etc.
- Pay particular attention to the drain. If ice builds up inside it could cause a blockage, restricting airflow. Ice can also cause cracks and permanent damage.
- Monitor the ambient temperature of the compressor room, it should be over 5⁰C. The ideal ambient temperature for an air compressor is between 5⁰C and 40⁰C.
- Check the operational running temperature of the compressor – it should be running between 65⁰C and 90⁰C.
- If you have a rotary screw compressor with a controller, then it will sense that the internal compressor temperature is too cold and does not start. Once the compressor is up and running the internal temperature will rise.
- Check oil levels frequently.
- Check that the compressor still loads and unloads correctly. When rubber seals get cold, they shrink and go hard. This can cause the intake valve seal not to work properly, stopping the compressor from loading.
- Adjust compressor ventilation to winter mode allowing the compressors heat to warm the ambient temperature.
- Install temperature-controlled heaters nearby. Ideally the ambient should not drop below 5⁰C.
- Ensure any external pipe work carries only dried, compressed air or is insulated.
- Check air intake openings to make sure there is adequate protection from increased rain (or snow) blowing in from outside.
- Install an auto drain or drain condensate daily.
- Insulate and/or heat drains, condensate traps and water lines.
- If possible, with smaller workshop compressors, move them to a warmer area.
- Research if your supplier provides a cold weather kit
- Ensure your machine is using compressor grade lubricant
If you are noticing or experiencing problems with your compressor system, concerned about how best to protect your compressed air supply through the cold winter months, looking for expert advice, or would like to be shown some simple winter checks that you can conduct yourself, please don’t hesitate to contact us!

